Tank Scaffolding
Tank scaffolding is a specific category of industrial scaffolding, which is utilized to access and perform work on large storage tanks primarily used in the oil & gas, chemical processing, and power generation industries. These tanks often exhibit one-off shapes and sizes, so tank scaffolding is designed to meet the specific needs of each tank to provide access safely and efficiently for maintenance, inspection, or repair work.
Types Of Tank Scaffolding
-
Modular Scaffolding
Modular scaffolding consists of many different modules, which can be adjusted to accommodate the configuration and size of the tank. The modules can be configured to adapt to complex curved surfaces, and it is useful in environments with limited space and changing tank shapes such as the inside or outside of reactors and towers.
-
Suspended Scaffolding
Suspended scaffolding systems are suspended on the top of the tank by steel cables or brackets. They are often used for inspection, cleaning or painting of the tank outer wall for large tanks. The suspended scaffolding system is best used at heights, especially when the scaffolding can not be supported from the ground, and are typically considered a very safe and efficient method of access.
-
Mobile scaffolding
Mobile scaffolding is a wheeled scaffold system that allows the scaffold to be moved on flat ground. They are most useful for the external maintenance of smaller tanks and probably used for shorter term projects, and situations that require moving the scaffold.
Advantages Of Tank Scaffolding
- Flexibility: Tank scaffolding can accommodate a variety of different tank shapes - cylindrical, spherical or asymmetrical. This flexibility means that workers can safely access all parts of a tank in even the most complicated section of a tank or vessel safely.
- Safety: Tank scaffolding provides workers with a stable and secure platform that is less likely to lead to a work-at-height incident in complicated industrial environments.
- Productivity: Tank scaffolding provides a more manageable way to perform worker tasks such as painting, welding or cleaning a tank to minimize downtime and improve productivity.
- Cost Effective: Tank scaffolding can be taken down and reused for other projects, making it a cheaper option for facilities that will be painting tanks or adjusting tank maintenance practices frequently.
Actual Construction Project Examples
Project 1: Repair Of Oil Storage Tanks In Saudi Arabia
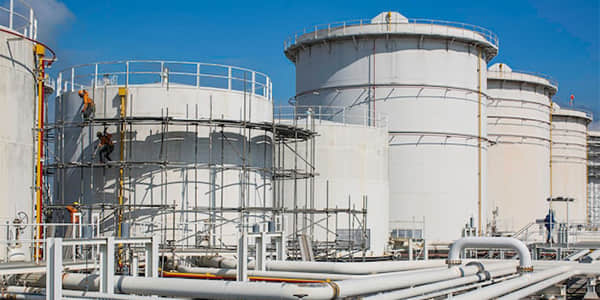
Location: Dhahran, Saudi Arabia
Backdrop: The oil storage facility in Dhahran, Saudi Arabia, is one of the largest in the region in that period of time having 10 crude oil storage tanks at a volume of 100,000 imperial gallons (about 378,500 litres) of storage. The storage tanks, after 15 years of usage needed to be checked and the surface repaired for safety and continued use.
Difficulties:
- The storage tanks stood 40 metres tall, 60 metres in diameter and the scaffolding needed to work at those extreme heights, and on a curved structural surface. Furthermore temperature levels during that time could be experienced in excess of 45 degrees Celsius during daylight hours, which posed challenges regarding safety of the scaffold and durability of resources.
Scaffolding Construction Solution:
- A ring lock scaffolding system was selected as a scaffold solution that would be compatible with the circular structure of the tanks. The total area of supported scaffolding was 1500 square meters and achieved multiple levels of access around the tank. Scaffolding components were purchased in a high-heat resistant material, and with the addition of overhead shade structures on the scaffold and a misting system, heat stroke was eliminated.
Results:
- The project was completed in 6 weeks, which was 1 week earlier than expected due to the scaffold. The scaffolding allowed over 120 workers to access the tanks safely with only 12 hours of downtime over the course of multiple days of sampling & inspection per tank. The tanks inspected were deemed structurally safe, while all coatings were protective and are expected to extend the life of these tanks for an additional decade.
Project 2: Tank Redevelopment In Germany
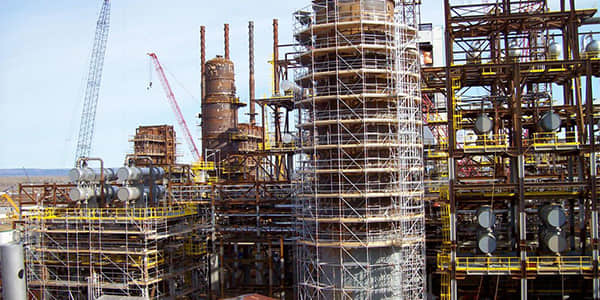
Location: Ludwigshafen, Germany
Summary: A chemical purposes plant with 15 storage tanks, each with a capacity of 5,000 – 10,000 cubic meters of hazardous materials, required an all-inclusive renovation owing to corrosion in some of the tanks. The storage tanks were critical to the operation of the plant that relied on the chemicals in the tanks to continue producing.
Issues:
- The tank spills were located in a very restricted area, but 3 meters apart from each other; hence, corralling scaffolding, again was a complicated undertaking. Moreover, since the tanks are directly exposed to chemicals, sulfuric acid to mention, the scaffolding systems need to be inert to corrosion and chemical damage. Finally, the plant operations could not cease, adding another layer of complexity to the coordination and operating system avoiding disruption.
Scaffolding-Based Solution:
- A dedicated cuplock scaffolding system was constructed, completely and thoroughly equipped with corrosion-resistant coatings on each part, in order to provide access to the tanks from all 360˚ over 1,200 square meters of total area. The space between the tanks was conducive to the scaffolding being erected with narrow gaps between, without interference from nearby tanks or works being conducted that required operational allowance of 2.5 m from access to the scaffolding. Workers accessed the scaffolding over five structurally reinforced access platforms with chemical-resistant flooring - flooring designed to resist exposure to the high-level chemical concentration in the tanks adjacent to the similar chemical exposure the workers were subjected to (ambient air).
Results:
- Renovation of five tanks was completed in three months, a duration extended by two weeks over the original schedule. The plant was in full operational mode for the entire duration of the project; there were no incidents of chemical exposure and/or serious accident. Corrosion was remediated, and a new anti-corrosive coating was reapplied that will sustain usability for an additional 15 years.
Project 3: LNG Tank Construction In South Korea
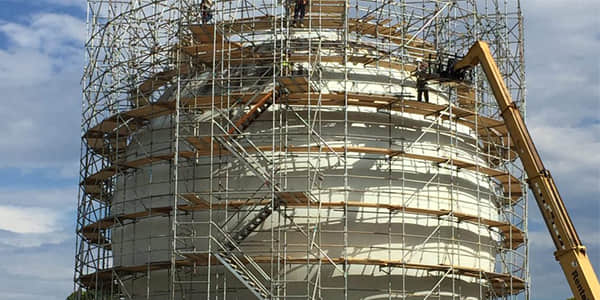
Location: Incheon, South Korea
Overview: A large thermos/storage tank system, this was 60 m high with a 70 m width built to store LNG at a temperature to or below -162°C and at a volume of 200,000 m3 on an LNG terminal site. As you might expect, a structure of this type has exceptionally high technical and structural requirements.
Challenges:
- The size and height of the tanks required a scaffolding system that would remain stable to handle extreme wind conditions they experienced ratings of winds (gusts) up to 80 km/h at times. Additionally, the scaffolding needed to allow for the simultaneous work of over 150 workers across different levels of the tank. Mother Nature sometimes proved to be a challenge as well with freezing weather and temperatures during winter months that compromised the stability of scaffolding and safety of the workers.
Scaffolding-Based Solution:
- An extensive heavy-duty frame scaffolding structure was implemented over a 3,500-square-meter area, supported by stranded steel anchors that were embedded 5 meters deep to withstand high winds. The design of the scaffolding was built with 12 levels with safety nets and materials approved for weather resistance and insulated coverings for worker protection against the elements. The platform design also customized for easy movement from internal to external surface areas to allow for expedient working of the tank.
Results:
- The scaffolding system ensured uninterrupted progress during the 10-month construction phase. Despite challenging weather conditions, the project was completed on schedule with zero safety incidents. The scaffolding’s stability enabled workers to safely and efficiently carry out complex welding, insulation, and pipe-fitting tasks, leading to the successful completion of the LNG tank, which is now fully operational and contributes to South Korea's growing LNG storage capacity.
Conclusion
As a key technology in industrial scaffolding, Tank Scaffolding has been widely used in aerial work and equipment maintenance in multiple industries. Through customized design, it can cope with different types of storage tanks, towers and other equipment, ensure construction safety and improve construction efficiency. In future industrial construction, Tank Scaffolding will continue to play its important role and provide reliable support for more projects.
I hope this article will help you understand the application and cases of Tank Scaffolding. If you have more questions or needs about scaffolding technology, please free to contact us!
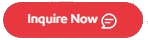
FAQ
Does the refinery scaffolding meet environmental protection requirements?
- The design of modern refinery scaffolding pays more and more attention to environmental protection, and many materials are recyclable. At the same time, the impact on the environment should be minimized during the construction of the scaffolding, such as reducing waste and construction noise.
How to ensure the safety of refinery scaffolding?
- Refinery scaffolding must comply with international safety standards (such as ISO, OSHA, etc.). Regularly check whether the structure of the scaffolding is damaged, and replace aging or corroded parts in time. At the same time, all operators need to undergo professional training.
How is the refinery scaffolding different from other industrial scaffolding?
- Refinery scaffolding usually needs to deal with more complex environments, such as high temperature, corrosive substances and special safety requirements. Therefore, it pays more attention to durability, safety and flexibility in design and material selection.